Specifying metal rainscreen assemblies
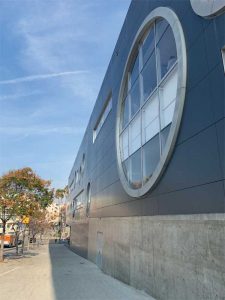
Photos courtesy IMETCO
Cladding
There are three broad categories of metal cladding—composites, insulated metal panels (IMPs), and single-skin. While IMPs attempt to combine all the four of the rainscreen components into one product, composites and single-skins have the four individual components in an assembly.
Manufacturers have been adding many options to these categories in the last decade, including the National Fire Protection Association (NFPA) 285, Standard Fire Test Method for Evaluation of Fire Propagation Characteristics of Exterior Wall Assemblies Containing Combustible Components, certifications, recycled content, long-lasting coatings, vented hat channels (to increase air movement), and hygrothermal warranties. The addition of products and accessories makes it increasingly challenging for architects and specification writers to understand what to use where and why.
Material selection
Selecting the right material for the job is essential when designing a building to last. Galvanized steel is the base material for most metal projects. It can provide great performance as long as it is not in a coastal area (within 457 m [1500 ft] of saltwater) or any other corrosive environment. It is not recommended to perforate galvanized steel because it will rust unless post painted. Galvanized steel also cannot be used with tight curved roofing.
While aluminum does not rust, it corrodes. The natural corrosion creates aluminum oxide, which helps protect the metal. Aluminum is slightly more expensive (10 percent) than galvanized steel, but offers many advantages including being lightweight (easy to handle and fast installations), flexible—it can create tight curves up to 1-m (4 1/2-ft) radius, is one of earth’s most common resources, and is recyclable.
Zinc is known more as an exotic material, but is highly corrosion resistant, can be easily worked, and will last a lifetime. After several years, zinc would patina into a soft bluish gray.
Copper, too, is an exotic material, can resist corrosion, and offers a unique look that will last for a lifetime.
Stainless steel is being used more and more for its unique resistance to saltwater, jet fuel, and other forms of chemical attack while providing a ‘polished’ look that will slightly dull over time.
Composites
The first category of metal cladding is composite. There are several acronyms for composite panels, and they can be made out of many materials. Composite panels are created by taking two light-gauge metal panels and adding some sort of ‘glue.’ Each manufacturer uses their own proprietary formulation of ‘glue,’ but they are all some sort of resin that permanently adheres the two panels together. Aluminum composite material (ACM), or better known today as metal composite material (MCM), incorporates not only aluminum, but also zinc, copper, stainless steel, and titanium. These composite panels can be manufactured in large sizes that will stay flat and smooth without any oil canning or bending. They can be the most expensive option of the three cladding systems. Further, adding NFPA-285 certification or small module sizes can increase the cost, too. Unlike IMPs, MCM panels are used as the exterior portion of a rainscreen, so other layers of ci and an A/WB are required to complete the assembly. While MCM panels can be recycled, they rarely are due to the high energy cost involved in the process. When considering the representative carbon footprint of a product, MCM panels are relatively high when compared with the traditional single-skin products.
Composite panels are a great option for column covers and curving. Custom modules or shapes are difficult to create, so many projects utilize traditional geometries such as simple curves, rectangles, or squares. Modifications in the field can be difficult. Availability of custom colors and exotic materials such as copper or zinc is limited. Warranties are typically limited to finishes and do not include waterproofing integrity or full-system warranties. It is important to remember long-term waterproofing performance is highly dependent on craftsmanship and field-applied sealant and caulk. Also, be mindful of panels not made in the U.S., as these imports, in the author’s experience, have been known to produce less-than-ideal long-term results.