Thinking Big: Seven considerations when specifying large insulating glass units
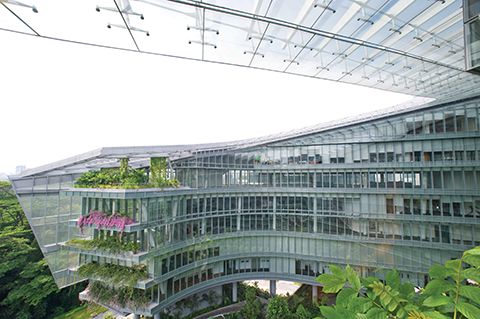
5. Fabrication
Whether processed manually or on ultra-sophisticated automated assembly lines, large IG units present challenging issues architects need to discuss with glazing contractors and glass fabricators. Before awarding a project, one should ensure suppliers have safeguards for dealing with the following:
- handling and placement of spacers that are highly flexible due to their large size;
- ruptures in spacer welds and seals caused by large-spacer flexibility;
- uniformity and press of primary seals;
- consistent production and orientation of heat-treated glass to both minimize reflective distortion, and avoid damage to glass and/or coated surfaces inside the sealed air/gas cavity due to contact caused by process-related glass-bowing;
- handling of large glass units; and
- safe storage and handling to prevent damage to, or failure of, primary sealant due to sheering stresses associated with large IG units.

6. Field-related issues
Careful handling and storage of glass is paramount on any jobsite, but especially so with large IG units because of their size and expense. Again, architects are well-served to address shipping, handling, and storage issues with glass fabricators and contactors as part of the bidding and specification processes, including:
- personal safety—one must ensure adequate labor power and proper equipment will be available to keep the worksite safe;
- primary seal protection—protocols need to minimize the risk for damage to, or failure of, the primary IG unit seal caused by shearing stresses during handling and storage;
- handling-related glass damage—acknowledging large IG units are more likely to be damaged during handling due to their size, one must work with the glass supplier to accommodate such eventualities; and
- glass-to-glass contact—a contingency plan should address latent damage to large IG units caused by glass-to-glass contact when subjected to changes in temperature and/or barometric pressure.
7. Glazing issues
As with shipping and handling procedures, glazing systems themselves must be properly designed to accommodate large IG units. For instance, metal members must effectively support and retain the unit’s weight, and setting blocks must be properly sized and located to support its weight as well.
Large IG units also should be designed to prevent excessive deflection of the horizontal sill, which can cause water to accumulate in the center of the unit and hinder good drainage through the weep system. Excessive deflection of adjacent horizontal members should be avoided to minimize the potential for glass damage and breakage.
More information about standard industry glazing practice guidelines are published in the Insulating Glass Manufacturers Alliance (IGMA) North American Glazing Guidelines for Sealed Insulating Glass Units for Commercial and Residential Use, and the Glass Association of North America’s GANA Glazing Manual.
Conclusion
Architects favor glass because of its unparalleled aesthetic and performance advantages. No other material can provide building occupants and building owners with such an enviable combination of views, daylighting and environmental performance. Building designs that incorporate large insulated glass units highlight those benefits. Along with more sophisticated design and manufacturing capabilities, this explains their increased popularity.
By working closely with glass suppliers experienced with large IG units to address the issues outlined above, architects and building owners can reap the rewards of these extraordinary products while minimizing potential headaches throughout design, production, shipping, handling and installation.
Steve Marino is a technical support manager at PPG Flat Glass, and has been with PPG Industries for 30 years, holding various positions in manufacturing and quality for both automotive and architecture glazing. Marino is an active participating member of both the Insulating Glass Manufacturers Alliance (IGMA) and Glass Association of North America (GANA), and sits on multiple committees and task groups for both organizations. He chairs GANA’s Tempering Division Technical Services Committee. Marino can be reached at smarino@ppg.com.