What’s wrong with my precast concrete garage?
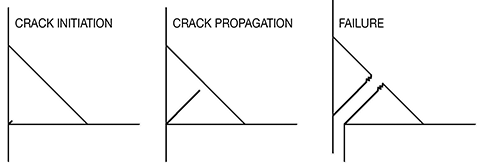
3. Failure
When the strength of the remaining intact cross-section is insufficient to withstand the applied load, failure occurs. It is typically abrupt—the weld severs completely, all at once, along a thin line at the outer face of the weld (Figure 5).
While it may seem as though such acute failure would require sustained and intense loading, it is a characteristic of fatigue that crack initiation and propagation need not occur at high stress. The main factors leading to fatigue failure are:
- number of cycles;
- severity of stress concentration created by surface defects and geometry of the detail; and
- stress range, or magnitude of the fluctuation in stress that occurs in each cycle.
In the case of stress reversal, this is the sum of the repeated tensile and compressive stresses.
Fatigue fractures are easily distinguished from other failures by their appearance. The failure surface typically has two distinct regions created during the crack propagation and failure stages. The crack propagation stage is characterized by a smooth, burnished appearance—the result of rubbing between crack surfaces during stress reversal.
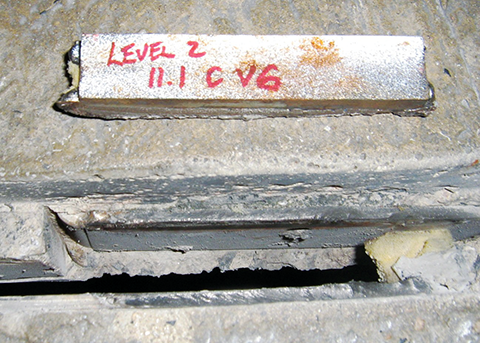
This burnished surface is accompanied by numerous linear marks (‘beach marks’) arranged in parallel; each of these striations represents an individual cycle of loading and chronicles a step in the crack-formation process. Additionally, fatigue fractures of double-tee connections typically exhibit a straight, uniform crack in the propagation zone, along with a thin fracture area at the weld face (Figure 5).
Figure 6 shows a flat bar-type flange connection that failed due to fatigue. In this photo (noting the erection bar is shown upside down), there is a straight and uniform crack-propagation zone, beach marks on the failed weld surface, and an abrupt fracture at the face.
Close review of the fracture surface reveals a burnished appearance with distinguishable beach marks. As these beach marks occur at the microscopic level, they become even more apparent at higher magnifications. Figure 7 shows scanning electron micrographs of the fracture surface of two typical connections. At the microscopic level, numerous parallel striations are clearly visible—each represents the point to which the metal fractured before stress reversal.

Code requirements
It is important to note while this connection is ubiquitous in the precast industry, review of model codes and industry standards finds a general caution against using this configuration when subject to fatigue loading. Specifically, American Institute of Steel Construction (AISC) Steel Design Guide 27, Structural Stainless Steel, cautions stress concentrations, eccentricities, and fillet welds should be avoided to eliminate fatigue problems.
Moreover, connections of this nature are outright prohibited by some authorities. Both American Welding Society (AWS) D1.6, Structural Welding Code–Stainless Steel, and the U.K. Steel Construction Institute’s Design Manual for Structural Stainless Steel state fillet welds should not be used in situations that produce bending moment about the longitudinal axis of the weld when such bending causes tension at the root of the weld. These guidelines underscore the importance of fatigue considerations in the design of precast double-tee connections, and provide an explanation for many of the failures observed in practice.
The International Building Code (IBC) largely defers to the American Institute of Steel Construction (AISC) 360, Specifications for Structural Steel Buildings, for design of welded connections. However, as precast connections are typically constructed of stainless steel, AISC 360, which pertains only to structural steel, does not directly apply. Nonetheless, AISC Steel Design Guide 27 states AISC 360 may be used as long as reduced resistance factors or increased factor of safety are considered.