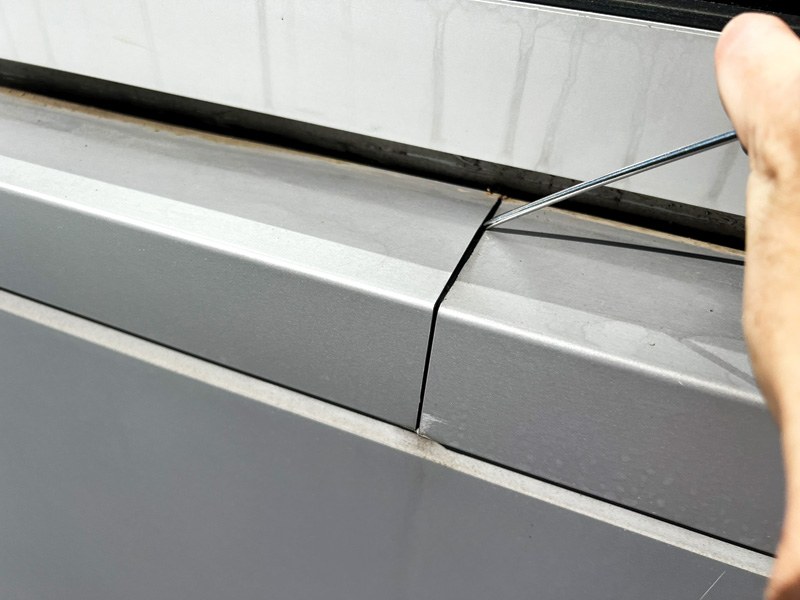
Coordinating the interface details of building enclosure systems is a common challenge during design and construction to ensure continuity of dedicated control layers (e.g. thermal, water-resistive air barriers [WRABs], etc.) between adjacent assemblies. This is particularly true where multiple trades are involved with the sequencing and installation of the various enclosure systems. In these cases, coordination of the transition trim components required to integrate the assemblies of different manufacturers properly is paramount.
While maintaining continuity of the dedicated control layers of the building enclosure is generally understood by the design profession, transitional components incorporated into the enclosure assembly are often overlooked during pre-installation coordination efforts. This is because these components are commonly viewed as an aesthetic element of a specific enclosure assembly that would not adversely affect the performance of an adjacent system or overall enclosure.
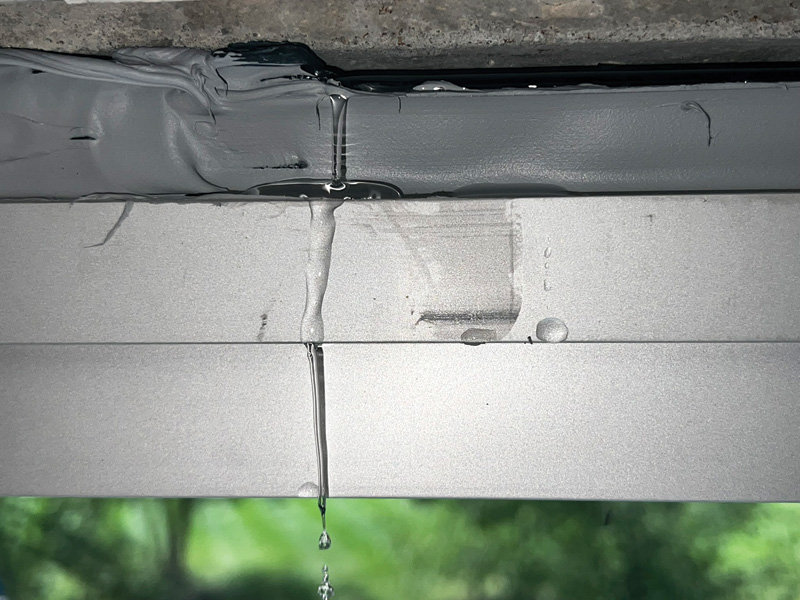
The challenge is that when trim elements are modified during pre-construction efforts to accommodate project-specific conditions better, the potential exists for the modifications to inadvertently deviate from the original design intent of the overall enclosure or tested assembly. Another difficulty is that trim elements may require enhanced coordination to ensure continuity of the surrounding control layers, depending on their relative position and detailing within the wall system. This may require a trim component to be installed separately from the surrounding system to facilitate proper integration. In these instances, trim components need to be designed and installed with the same rigor as the enclosure assemblies to ensure better intended performance. It is also important to note that while such components may appear functional in two-dimensional drawings, planar transitions, splice joints, terminations, etc., need to be fully understood, and appropriate details developed and reinforced during the shop drawing, mock-up, and installation phases of the building construction.
Some of the challenges mentioned above were encountered at a high-rise residential building where interface trim components of the metal panel cladding assembly were modified during construction in an attempt to simplify installation sequencing. In doing so, the trim component was extended into the rough opening of the adjacent aluminum-framed ribbon window system. This modification unintentionally interrupted the integration of the WRAB and aluminum-framed ribbon window system. As a result, the primary perimeter sealant for the window system was bonded to the leg of the metal trim within the rough opening rather than the WRAB, as originally designed. Due to installation sequencing, termination, and splice joint challenges, the trim utilized bed seals to ensure watertightness. Shortly after occupancy, widespread water leakage was reported along the windows. Investigative efforts determined that the bed seals were not continuous, which provided a direct pathway for water to bypass the control layer and enter the building.
Authors
Jeffrey Sutterlin, PE, is an architectural engineer and associate principal with Wiss, Janney, Elstner Associates (WJE) in the New York/Princeton office. He specializes in the design, investigation, and repair of building enclosures. He can be reached at jsutterlin@wje.com.
Jonathan Jadico is an architectural engineer and senior associate with Wiss, Janney, Elstner Associates (WJE) in Princeton, New Jersey. He specializes in the investigation and repair of building enclosures. He can be reached at jjadico@wje.com