Aluminum curtain wall coatings on 21st century façades

Aluminum pretreatment
When pure aluminum corrodes, the result is aluminum oxide, a hard substance that forms a barrier on the aluminum surface and protects against further corrosion. However, architectural aluminum is usually an alloy, with magnesium (with or without silicon) being typical additives. Magnesium is added to allow tempering through heat treatment; silicon is added to increase flowability during extruding. When magnesium is present, magnesium oxide becomes a part of the film found on the surface of the aluminum. Magnesium is very reactive and dissolves in anything with a pH lower than 11. (Silicon oxide, on the other hand,
can be very inert and only dissolves in fluoride containing acids.)
Further, heat-treating aluminum alloys change their characteristics by forming a thin subsurface layer. The layer contains a higher concentration of alloying ingredients since the tempering causes a flow of alloying elements outward along the grain boundaries. The oxidized surface of an aluminum substrate is generally imperfect, with pores and other defects. Unless proper pretreatment takes place, corrosion of the building fenestration or cladding can occur when it is exposed to moisture and corrosive compounds.
Pretreatment methods include conversion coatings—part of the surface is converted into the coating using a chemical or electro-chemical process—or ‘dry-in-place’ coatings, in which non-reactive substances are applied in a thin film on the metal. A long-standing method of pretreatment is a conversion coating using chromium phosphate. Typically, the metal is first cleaned and slightly etched (with a surface removal of <0.5 g/m2 [<0.0001 lb/sf]) to help create an even conversion layer. Then the metal is rinsed, and the chromium is applied and rinsed off. The result is a conversion layer of about 1 g/m2 (0.0002 lb/sf) of chromium phosphate. Unfortunately, the chromium process is hazardous, with byproducts including chromic acid (a carcinogen), hydrofluoric acid (a poison), and phosphoric acid (a water pollutant).
To eliminate the use of chromium in the pretreatment process, some methods involve aggressive aluminum etching. This can involve either etching with acid alone, or first using an alkaline etch and rinse, followed by an acid etch and rinse. Acid etching is often the preferred method because it easily dissolves the magnesium and silicon alloying elements, and the process results in the best use of water, ease of waste treatment, and surface appearance.
Tests have shown the 2 g/m2 (0.0004 lb/sf) of aluminum surface removed by etching improves coating adhesion and greatly reduces under paint filiform corrosion. Filiform corrosion is a localized form of corrosion that manifests in threadlike ‘tunnels’ visible under the coating surface. This amount of etching coincides with the removal of the subsurface layer, which is normally 3 µm (0.1 mils) in thickness.
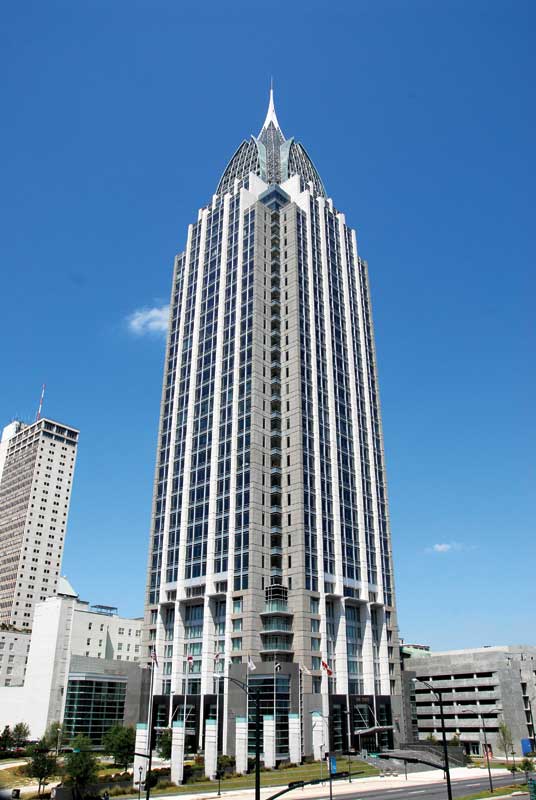
Determining coating performance
Coatings that meet the highest standards, as defined by third-party organizations, should be used on structures with large expanses of structural glazed systems. Additional considerations—such as environmental concerns, ease of use, and color requirements—should be carefully weighed during the design process so a client’s needs can be met and the long-term success of the skyscraper can be ensured.
The standards of the American Architectural Manufacturers Association (AAMA are voluntary and include specifications, performance requirements, and testing procedures for pigmented organic coatings on aluminum extrusions and panels (for factory-applied organic coatings only). As defined by the AAMA specifications:
- AAMA 2603, Basic Pigmented Coatings, identifies pigmented organic coatings that will provide a good level of performance, highlighted by one year of Southern Florida weathering with the test panel positioned at a 45 degree angle;
- AAMA 2604, High Performance Coatings, focuses on high-performance organic coatings that will provide and maintain a high level of performance requiring a five-year Southern Florida weathering; and
- AAMA 2605, Superior Coatings, focuses on organic coatings that will provide and maintain a superior level of performance requiring a 10-year Southern Florida exposure.
Coatings meeting the AAMA 2605 standard are appropriate for use on high-end building exteriors and are expected to last the lifetime of the building.