Aluminum curtain wall coatings on 21st century façades
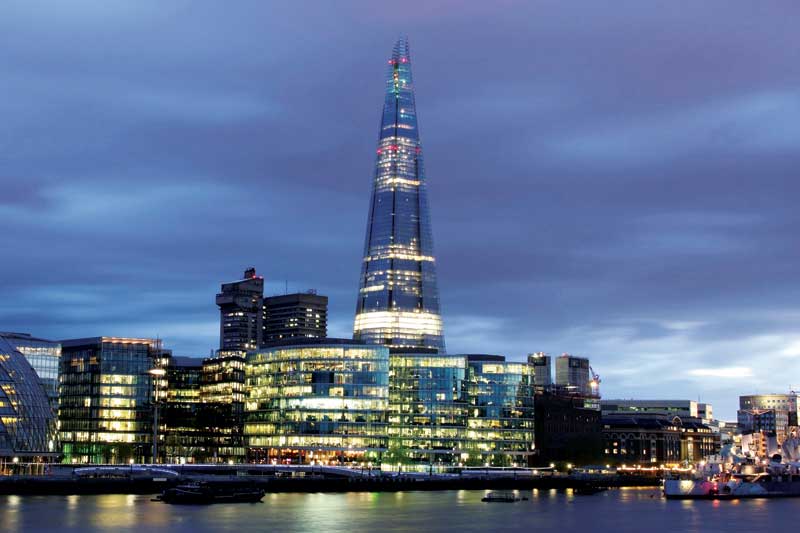
Testing procedures for coatings
Procedures for testing architectural coatings include both mechanical tests—for example, testing the physical properties and film integrity—and exposure testing. Some issues, such as coverage, fall within the purview of quality control and are therefore not within the scope of performance testing.
Tests may include:
- impact resistance;
- adhesion;
- chemical resistance;
- humidity;
- salt-spray resistance;
- mortar resistance;
- acid resistance; and
- pencil hardness.
However, the most significant factor influencing a coating’s long-term performance is its weatherability—particularly its resistance against ultraviolet (UV) light.
Laboratory tests of painted panels conducted within cabinets using an artificial light source to simulate sunlight can provide some measure of a coating’s UV resistance. However, the most complete results are obtained in natural environments that provide exposure to the full spectrum of light in combination with other factors such as condensation, biological growth, and physical erosion not recreated in a laboratory cabinet.
Data from weather testing performed in Southern Florida is considered to be the global ‘gold standard’ of testing data. The subtropical climate in the region provides natural, realistic exposure to product specimens, yet results can be achieved on an accelerated timeline because one year of the region’s sunshine and moisture can equate to several years of exposure for other parts of the globe. The 45-degree south-facing exposure also makes the exposure more severe. The state offers high annual UV, high year-round temperatures, abundant rainfall, and very high humidity. Southern Florida exposure data is mandatory for AAMA (as well as for other quality organizations around the world).
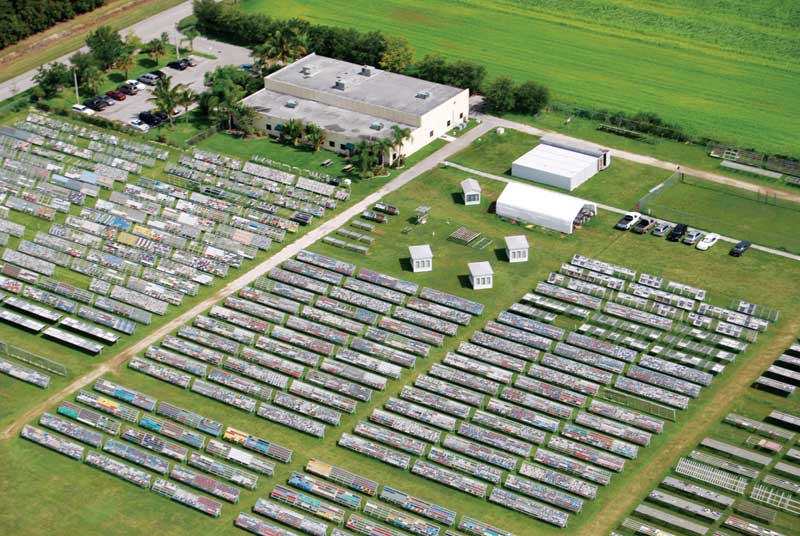
AAMA 2603, 2604, and 2605 specify weathering testing involves exposing samples representing typical products on an exposure rack in Southern Florida south of latitude 27 degrees, north at a 45-degree angle, facing south, and inland at least 3.2 km (1.9 mi). At the end of the test periods, samples are evaluated for:
- film integrity;
- color retention;
- chalk resistance;
- gloss retention; and
- erosion resistance.
Florida is home to the largest outdoor weathering testing facility in the world. Various specimen mounting and exposure techniques are used to obtain accurate results; tests on exterior-use coatings are conducted using direct exposure. Test panels are mounted directly facing the sun, with varying angles and mounting techniques.
Coatings manufacturers usually work directly with a lab, conducting a series of tests that will provide the most complete set of data for a given product. Specimens are typically sent to the lab directly from the manufacturer’s research and development group. The testing lab then conducts the exposures and issues progress reports to the manufacturer. All testing is ‘blind’ so there is no bias in the data from the testing lab. Manufacturers then provide customers with the test data.
In an effort to collect more data faster, testing facilities are branching into different locations and different types of testing. Exposure facilities in the Arizona desert offer about 20 percent more sunlight, higher annual temperatures, and lower humidity than is typical in Florida. The increased UV and the extreme dry heat make Arizona the ideal location for testing highly durable materials intended for use in deserts around the world.