Channel High Design: Specifying channel glass systems to enhance modern buildings
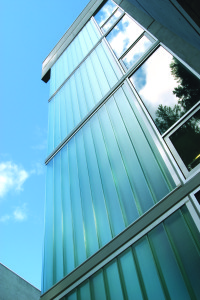
Stepped transitions
One emerging trend is to arrange channel glass in a vertical or horizontal pattern separated by windows, doors, or framing units to create a sense of movement and interest in a linear plane. In other instances, it is necessary for the channel glass to work around HVAC or other building system mechanics. Channel glass is versatile enough to step around these in fixed objects defined by the glass widths (otherwise known as stepped transitions), with appropriate planning.
Since channel glass is fabricated in a fixed module width, it is rare for the planks to lie around an object without interference. Cutting the channel glass precisely around the object is not a viable option since the inside corners or notches created during this process place higher stress on the corner and increase its chance of failure.
To achieve the desired layout, the design team can use flange cut pieces (i.e. L-shaped pieces of channel glass) and a combination of different standardly available widths to achieve the appropriate configuration. The installation team can also adjust the glass at the head or jamb since the extruded aluminum perimeter frame typically allows for flexibility in glass bite (i.e. how much of the available space in the frame is taken up by the glazing).
While there is almost always a design solution using channel glass in stepped transitions, one should consider engaging the manufacturer or supplier during the design phase. Suppliers can provide design support and guide the installation process to streamline time and reduce waste.
Raked heads and sills
Another option when using channel glass to enhance a building’s form is to incorporate raked heads and sills. In these instances, the head and sill of the cast-glass channels change elevation gradually across their width. They make it possible for design professionals to break out of the typical, linear channel glass mold and create vertical applications with angles and curves, such as trapezoids.
Since raked heads and sills have varying elevations, the individual channel glass segments are cut on an angle to fit the opening. During this process, the entire plank is cut, rather than the inside corner, to ensure the glass segment is not at risk for failure. Since it causes the left and right sides of the glass to be different lengths, it is important to avoid errors in the surrounding opening size or frame placement to ensure the glass is secure, plumb, and properly fitted.
Vertical fins
Another growing trend is to orient channel glass as vertical fins on buildings. In such instances, the planks, or ‘fins’ protrude perpendicularly from the flat face of the building for privacy or to create aesthetic interest. Since the fins are a decorative, rather than structural, element of the building, engineers typically calculate and treat them as a ‘corner condition,’ even if they are located in the middle of a wall far from a corner zone. Glass calculated to accommodate higher stress loads typically results in lower allowable glass spans and often requires greater frequency of anchor locations on the framing. Treating fins in this manner ensures they are stable as the pressure increases when the wind moves directly at and around them.
Conclusion
As channel glass continues to evolve, new shapes, patterns, and configurations will emerge to push the material to new limits. Channel glass suppliers can be contacted for more information on the resources and design support they can provide. In Part Two of this series, the author will explore installations of channel glass in curved and serpentine walls; Part Three will delve into high-performance systems that address meeting hurricane, sound, and thermal insulation requirements.
Jeff Razwick is the president of Technical Glass Products (TGP), a supplier of fire-rated glass and framing systems, and other specialty architectural glazing. He writes frequently about the design and specification of glazing for institutional and commercial buildings. Razwick is a past-chair of the Glass Association of North America’s (GANA) Fire-Rated Glazing Council (FRGC). He can be contacted via e-mail at jeffr@fireglass.com.