Extruded polystyrene in protected membrane roof assemblies
Photovoltaic (PV) panel assemblies are readily installed on top of buildings with PMRAs. The structural components above the waterproofing membrane provide a foundation for the framework that supports the solar assembly. Penetrations of the membrane and deck can be avoided using a PMRA as the firm foundation for PV panels.
PMRAs require competent engineering to accommodate the dead and live loads on the insulation. Specifiers must also consider the buoyancy of the insulation. (XPS insulation floats quite well in water.) Nonetheless, a properly designed PMRA is a versatile roof, offering many advantages to a building owner. PMRA designs are continually being improved upon and are growing in popularity.
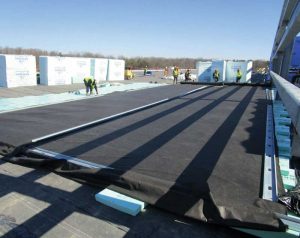
Using XPS insulation in PMRAs
The simplest PMRA consists of: (1) a waterproofing membrane installed on a concrete deck or other appropriate substrate; (2) XPS insulation boards placed on top of the membrane; and (3) ballast loaded on top of the XPS insulation boards (see Figure 3).
The insulation in roof assemblies provides long-term energy efficiency and resists applied structural loading. A properly specified roof assembly withstands compressive forces from dead loads and potential live loads and complies with fire classification requirements for the roof covering and the roof assembly. In addition to these requirements, insulation in PMRAs must deliver thermal performance while being exposed to Mother Nature’s moisture. A variety of insulation materials could meet performance requirements for commercial roof assemblies, but XPS is uniquely qualified for PMRA applications because it delivers long-term thermal performance even when exposed to moisture.
Ballast may consist of concrete pavers, aggregate, or even growth media in the case of a vegetative roof. Depending on the ballast, a fabric or other components may be installed above insulation and below the ballast. Specially designed layers also may be needed between the insulation and the membrane to provide separation for drainage as well as specialized protection (such as root barriers on vegetative roofs). Joints between XPS do not need to be sealed and in some cases it may be better to not seal the joints to permit water vapor to escape the roof assembly. For PMRAs roofs, XPS is not the air barrier or the water resistive barrier, rather, it acts as the thermal barrier for the roof. Regardless, the XPS should be installed in accordance with the manufacturers instructions for the application.
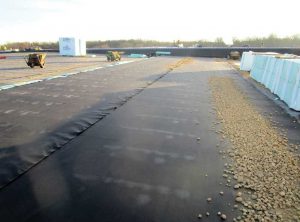
A key part of a PMRA design is the specification of the insulation boards. Since the earliest use of protected membranes, dating back to the 1950s, it was recognized extruded polystyrene (XPS) is uniquely well-suited for this application. The roof covering, of course, is protected by the insulation boards and not vice versa; hence, the insulation boards are exposed to moisture. They become wet and do not dry out quickly because the water typically collects just above the roof covering before it is drained. Evaporation of moisture from the roof is slowed because the insulation layer blocks sunlight and lowers the temperature of the roof covering.
In the half-century since PMRAs were first developed, the superior moisture resistance of XPS has been well documented. XPS is a hydrophobic material, which means water will bead up and run off its surface. XPS resists moisture absorption much better than expanded polystyrene (EPS) foams. A recent white paper from the Extruded Polystyrene Association (XPSA) analyzes the effects of long-term exposure to moisture on the thermal performance of polystyrene insulation. The continuous microstructure of XPS resists the absorption of water into the insulation. Consequently, XPS is more resistant to moisture penetration and related freeze-thaw damage compared to other insulation materials.
An important property of interest for the roof’s design would be determination of the total R-value required for the climate zone, which would then dictate the thickness of XPS. For more on climate zones, see American Society of Heating, Refrigerating and Air-Conditioning Engineers
(ASHRAE) 90.15 and the International Energy Conservation Code (IECC)6 (see Table 1) XPS provides a high R-value per inch (R-5) along with excellent moisture resistance.
Table 1. Descriptions of Climate Zones
International Energy Conservation Code (IECC) | |
Subarctic | Zone 8 |
Very Cold | Zone 7 |
Cold | Zone 5 and 6 |
Mixed-Humid | 4A and 3A counties above warm-humid line |
Mixed-Dry | Zone 4B |
Hot-Humid | 2A and 3A counties below warm-humid line |
Hot-Dry | Zone 3B |
Very Hot – Humid | Zone 1A |
Marine | All counties with a ‘C’ moisture regime |
The choice of XPS ‘type’ for PMRA systems is dictated by the compressive strength that is required for the PMRA application to withstand the loads expected on the roof. These dead- and live-loads may include auxiliary equipment and vegetation as well as foot traffic and vehicular traffic. XPS is classified by ASTM C5787 CAN/ULC-S701.18 into types by compressive strength. PMRA system designers would specify XPS type(s) with compressive strengths high enough to withstand the expected loads.