Extruded polystyrene in protected membrane roof assemblies
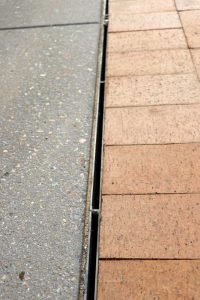
The properties of XPS insulations can be varied by the manufacturing process. By varying the cell wall thicknesses between internal cells, the density and strength of the extruded polystyrene foam can be varied over quite a large range. It is interesting that for many types of extruded polystyrene insulation the moisture absorption and R-value per inch are not affected much by the ASTM type. For example, types IV, V, VI, and VII all have the same R-value per inch and the same low moisture absorption value. Yet their densities and strength vary quite a lot.
As classified in ASTM C578 and measured by ASTM C303,12 the minimum densities of XPS types are as follows, in kg/m3 (pcf):
∞ Type IV – 23 (1.45);
∞ Type VI – 29 (1.80);
∞ Type VII – 35 (2.20); and
∞ Type V – 48 (3.00).
As classified in ASTM C578 and measured by ASTM D1621,13 the minimum compressive strengths of XPS types are as follows, in kPa (psi):
∞Type IV – 173 (25.0);
∞ Type VI – 276 (40.0);
∞ Type VII – 414 (60.0); and
∞ Type V – 690 (100.0).
As a rule, higher density correlates with higher strength in XPS insulation board. Types VII and V are suitable for applications that may have high point loads, e.g. applications with raised pavers or PV arrays. Type V is capable of withstanding high loads such as what may be experienced with vehicle parking on the building’s rooftop.
XPS types IV, VI, VII, or V each would be suitable for a typical ballasted PMRA. More ballast or ballast securement may be required for high wind zones and, as a result, higher compressive strength. The International Building Code (IBC) requires ballast designs be in accordance with ASNI/SPRI RP-4.11
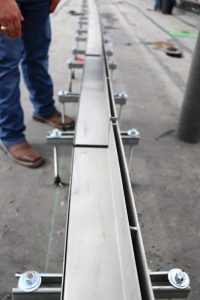
A roof assembly’s fire classification is a very important factor. The discussion of roof assembly fire classification is beyond the scope of this article. Specifiers are referred to ASTM E10812 or UL79013 for more about fire classification.
The overall thermal resistance of the PMRA is improved with effective drainage. Ponded water between the insulation and the membrane for long time periods could contribute to moisture absorption, which even for XPS would require R-value adjustments. For this reason and others, drainage systems are essential in most designs of PMRAs even when using XPS insulation. A PMRA typically allows for drainage between the roof covering and the XPS insulation board. A drainage gap can be accomplished with a perforated or dimpled mat made of polyethylene, rubber, or a composite material; or the XPS itself could contain channels, slots, or kerfs to aid in drainage.
There are many considerations in the design of PMRA: structural performance, wind uplift resistance, means of egress for occupiable roofs, and other factors. Fortunately, much knowledge and experience has accumulated in recent years and more and more contractors and building materials suppliers are knowledgeable of standards and best practices.
Published guidance has been developed about PMRA and is still evolving. The interested architect or designer is encouraged to contact one or more of the XPS manufacturers for recommendations on designing a PMRA that will provide maximum durability and performance.
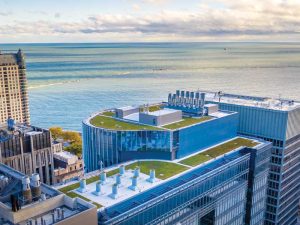
Thermal resistance and structural integrity
Specifiers of the components of PMRAs must balance form and function with a high degree of knowledge of PMRA components.
Below the insulation, the roof covering installed to the deck and a suitable drainage system regulates the water retention;
The insulation itself is thick enough to provide the desired amount of thermal resistance; and
Above the insulation, the ballast holds down the XPS, which must be strong enough to withstand the weight of the ballast as well as variable loads such as rainfall and human or vehicular traffic.
XPS floats on water. If there are several inches of water on the roof because of a sudden downpour, then hydrostatics requires the weight of the volume of displaced water be countered with at least the same weight in ballast. Hydrostatics tells how much ballast is necessary to keep the XPS from floating.
Ballast is used to provide uplift resistance for roof assemblies that are not adhered or mechanically attached to the roof deck. However, buoyancy is not the only factor in determining the ballast requirement. The PMRA must meet standards relating to wind uplift resistance. The height of the parapet wall surrounding the PMRA has a striking effect on wind uplift. For a detailed discussion of ballast design requirements, refer to ASNI/SPRI RP-4.11