Fast-setting success for tropical climates
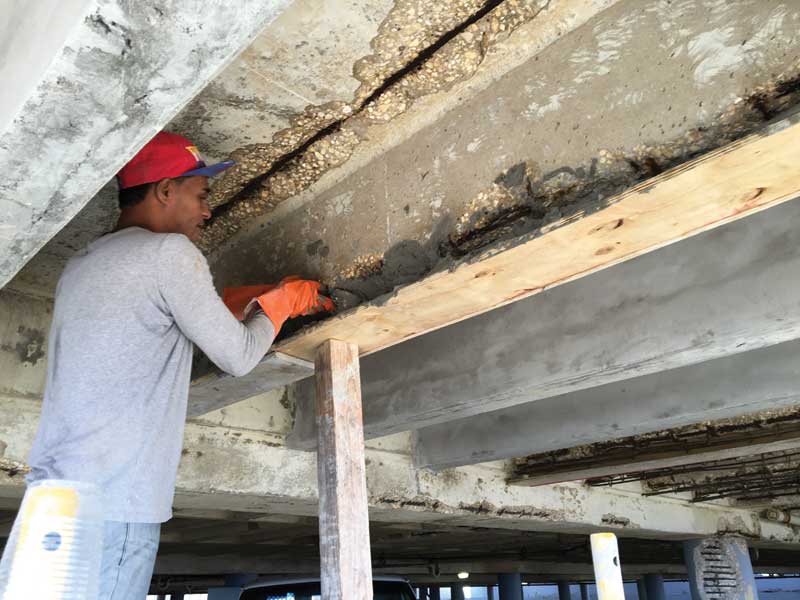
Minimizing traffic disruption
The Teodoro Moscoso Bridge is the longest bridge spanning a body of water in Puerto Rico. The four-lane, 2-km (1 ½-mi) long toll bridge spans the San José Lagoon, connecting the cities of San Juan and Carolina while also serving as the main entrance to the Luis Munoz Marin International Airport. With the airport on one end and a premier shopping destination (the Mall of San Juan) on the other, the 23-year-old bridge is subjected to a high level of vehicular traffic. Its total length, including access roadways, is 3 km (2 mi).
In summer 2015, Albertis—the private company that manages and maintains the bridge—began a comprehensive rehabilitation program involving various levels of repair. The goal was to perform repairs with minimal road closures for drivers.
The contractor recommended several single-component, fast-setting hydraulic cement products that would allow Albertis’ maintenance crew to restore the bridge faster and reduce downtime. These products’ ability to harden quickly and achieve high early strength, even while underwater, also allowed the crew to work through flash rains—which are common in the summer rainy season—without compromising strength and durability. Repairs were accomplished in three separate phases.
Phase 1–Partial-depth repairs
Since the top rebar in areas of the pavement near the toll plaza did not have enough concrete cover, it was attacked by the high concentration of chlorides in the environment. In turn, this caused deep cracks and fragmentation in the concrete. To minimize road closure time, the crew needed a very fast-setting structural mortar with early high strength to perform the partial-depth repairs.
A mix especially made for harsh environments was chosen, consisting of rapid-hardening cement, specialty sand, and high-performance additives. An integral, powder-based corrosion-inhibiting additive was introduced to create a protective barrier on the embedded steel that both repels water and reduces chloride migration to the rebar. The crew was able to open all lanes to traffic three hours after repairs were made, which meant minimal interruption to the operation of the toll plaza.
“Using the rapid-setting product really made the difference,” says Juan Matos Ostolaza, the bridge’s operation manager.
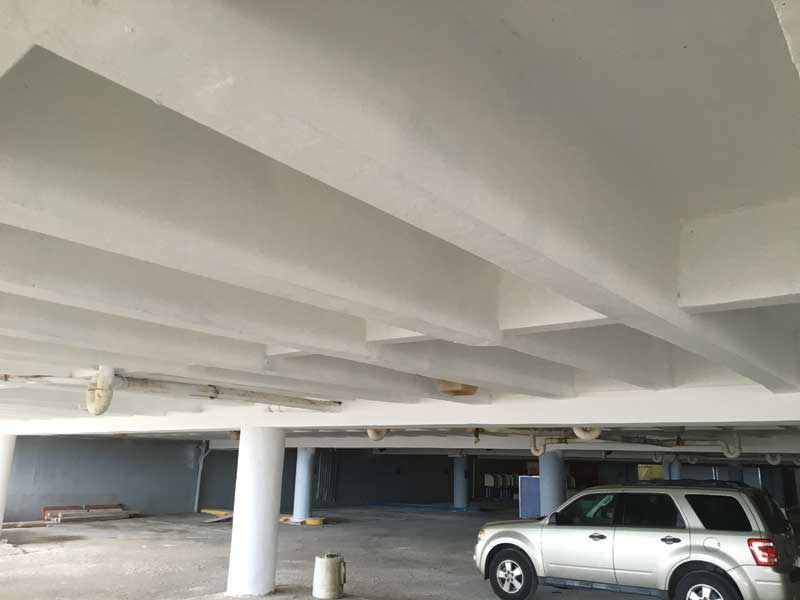
Phase 2–Lateral-barrier repair
The bridge’s lateral barriers were at least 23 years old, with concrete delamination spalling (also due to corrosion from chlorides) quite evident in numerous areas. All damaged areas were scattered spots—isolated zones approximately 1×1 m and 2×2 m (5×5 ft and 8×8 ft) in size—so the bridge needed a durable, yet aesthetically pleasing solution that would blend well with the existing concrete.
For these vertical partial-depth repairs, the contractor recommended the same corrosion-resistant V/O repair material used in the National College University project. Tinted gray to match most Portland concrete surfaces, the material bonds well with existing concrete and is resistant to both freeze/thaw and corrosion. The integrally added corrosion-inhibitor contributes additional embedded-metal protection.
The crew finished the barrier surfaces with a thin layer of concrete-patching compound to provide a smooth surface ready to receive the anticarbonation protection coat. The concrete-patching material is formulated with a premium-grade fast-setting cement, high-performance polymers, and a finely ground aggregate. It is suitable for moist environments.
The original plan was to repair 91 m (300 ft) of barrier, but once the bridge’s management team discovered how quickly and easily the crew could perform repairs, it extended the work to 2414 m (7920 ft) of barrier. Soon after, the decision was made to repair the other side of the bridge (another 2414 m) and the toll plaza structure. In the end, the crew repaired more than 7620 m (25,000 ft) of concrete barriers.
“It was great to see the crew working with materials that allowed them to complete repairs in a highly efficient manner,” says Matos Ostolaza.