Grasping non-penetrating fall protection guardrail systems
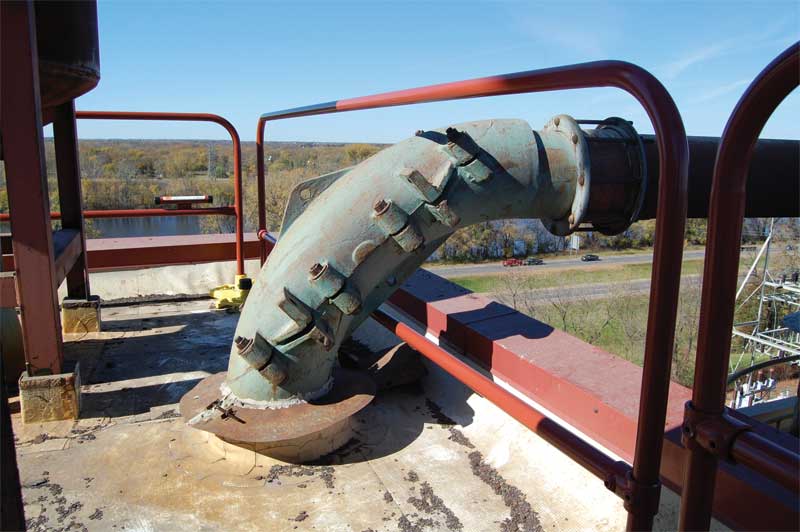
Ease of installation
Non-penetrating guardrails are designed to be assembled and disassembled as needed. Generally, their installation can be summed up in three steps:
- Place the bases at their intended positions.
- Insert the rails into the base’s built-in ports.
- Secure the rails into the ports.
The installation’s difficulty depends on the type of guardrail used. If workers need to accommodate uneven surfaces or equipment, individually adjustable rails should be used, though they may take more time and labor to install.
Mobility
It is easy to transport non-penetrating guardrails from one place to another—a factor making them cost-effective and suitable for multiple construction projects over different locations. Some manufacturers even provide a special tool for this purpose.
Flexibility
Non-penetrating guardrails can be configured according to a project’s needs. This makes them suitable for a variety of buildings, including schools, offices, commercial spaces, government buildings, distribution centers, and manufacturing facilities.
OSHA compliance
When properly installed, non-penetrating guardrails provide an adequate amount of protection in compliance with OSHA’s guidelines. The qualities allowing them to meet those requirements are the placement of the top rails and mid-rails, the ballasted bases, and rails used as returns or outriggers at each start and end of the run. Rail sections that are used as outriggers stabilize the last portion of the rail section so it meets the 90-kg (200-lb) requirement.
Examining non-penetrating guardrail systems
As their name suggests, non-penetrating guardrails avoid penetration of the structures on which they are installed. They use a ballast or counterweight system to hold the guardrail in place instead of drilled structures.
Non-penetrating guardrails are typically used by maintenance personnel, contractors, inspectors, and workers with similar occupations. However, they are not intended for use with general public systems.
System limitations
Like all fall protection systems, non-penetrating guardrails have their advantages and limitations. Design/construction professionals should consider:
- Initial installation costs can be higher for non-penetrating guardrails than they are for other fall protection systems. The starting cost has been quoted as $50/ft, with 16 hours of work required for every 183 m (600 ft).
- Some surfaces are unsuitable for non-penetrating guardrails, no matter how adjustable the rails may be. Areas where the base support system cannot stay straight, for example, are off-limits to this system. Using bases is not recommended where the roof slope exceeds five degrees.
- If low-quality guardrails are used, or if they are improperly installed, they might not provide as much protection against falls as permanent railing systems. To prevent this, specifications need to be as detailed as possible.
Outside these concerns, non-penetrating guardrails involves little risk. They can be installed by personnel with only basic training, require minimal maintenance, and tend to be more cost-effective over the long run than their more-permanent counterparts.
Meeting OSHA requirements
Regardless of a fall protection system’s purpose, manufacturer, or other qualities, it must comply with OSHA’s guidelines. This can be ensured in a variety of ways.
- Every floor opening on stairways, ladderways, hatchways, chutes, skylights, pits, trapdoors, manholes, and similar surfaces should be protected by a standard railing. Exceptions can be made
in cases where the railing will interfere with construction work. - Every open-sided floor 1 m (4 ft) or more above an adjacent floor must be protected, except entrances to fixed ladders, stairways, or ramps. For these, separate safety protocols should be in place.
- Rails must be able to withstand 90 kg (200 lb) of pressure at any point in any direction. Any deflections of the rail under this load should not exceed 50 mm (2 in.).
- Any rail must have a vertical height of 1066 mm
(42 in.) between the top of the rail and the platform where it sits. Similarly, any mid-rail should have
a vertical height of 533 mm (21 in.), and the stanchion spacing must be at 2.5-m (8-ft) intervals.
These standards are set out under:
- OSHA 1910.23, Guarding Floor and Wall Openings and Holes;
- OSHA 1926.500, Scope, Applications, and Definitions Applicable to Fall Protection;
- OSHA 1926.501;
- OSHA 1926.502; and
- OSHA 1926.503.
They must be included or referenced in the quality assurance section of guardrail specifications. Again, however, they are general requirements, and OSHA is not obligated to approve railings complying with them.