Grasping non-penetrating fall protection guardrail systems
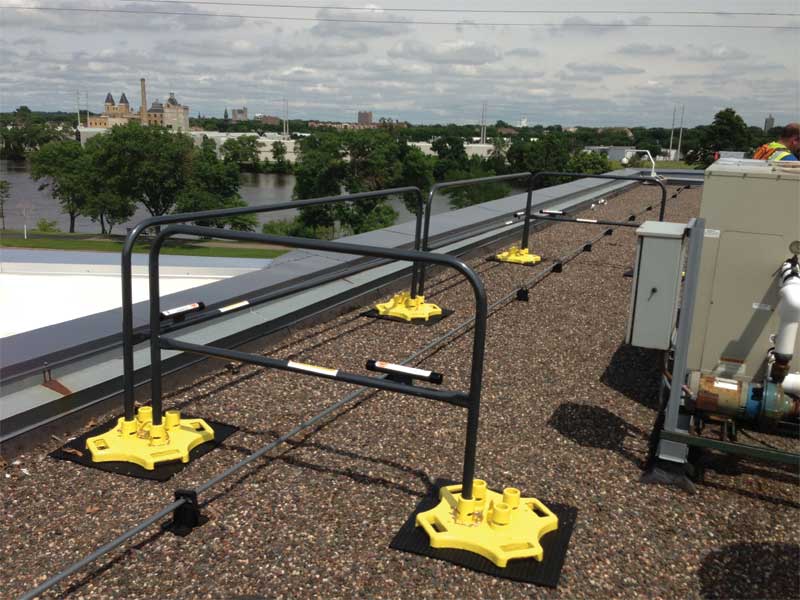
Architectural and owner requirements
In addition to basic safety, contractors should consider architectural intent and owner requirements when installing non-penetrating guardrails. These can include:
1. Areas to be covered
Ideally, fall protection systems should cover an entire roof edge, but as this is not always economically feasible, care must be taken to choose the best areas to protect (e.g. HVAC equipment, ventilation systems, surveillance cameras, and roof drain cleanouts). It is recommended an EHS or safety specialist be enlisted to review the fall protection plan. However, even with an EHS on board, the contractor may still be unclear on where to install guardrails—for instance, if the written specifications indicate the location of the fall protection system, but the drawings do not. If issues like these are not addressed, disagreements can occur between the EHS and contractor, compromising worker safety and wellbeing.
2. Aesthetics
A fall protection system must be compatible with the design intent of the building. For example, the owner of an industrial facility may wish to use a highly visible yellow system to indicate a commitment to safety, while a downtown library with a vegetative roof might require a less obtrusive railing blending into the building’s architecture. There is nothing in OSHA standards denoting a situation where safety yellow is required—manufacturers provide rails in this hue to provide an additional safety element.
3. Placement of roof attachments
The parts attaching the guardrails to the roof must be carefully placed and meet load requirements. An engineering analysis should be conducted to ensure the railing meets OSHA standards.
4. Materials
Compared to permanent rail systems fabricated with metal, ballasted non-penetrating guardrails are less expensive over a long-term period. The type of material should also be considered in relation to the other criteria previously mentioned above. Non-penetrating systems are generally made of steel or cast steel (bases) with either a painted finish or galvanized finish, but at least one manufacturer offers polyvinyl chloride (PVC). Generally, many permanent, fixed-type railings are made from aluminum and some steel. With these types of systems, the railing connections often need to be coped and welded.
Beyond OSHA compliance
Manufacturer specifications and compliance with OSHA standards are not the only considerations for specifying non-penetrating guardrails.
Types of non-penetrating guardrails
Non-penetrating guardrails feature two primary types of railing system: sized rail sections and mechanically assembled systems. Mid-rails are welded on sized rail sections, while mechanically assembled systems use fittings secured by fasteners. Also, sized rail sections are prefabricated from structural steel tubing at fixed lengths ranging from 0.9 to 3 m (3 to 10 ft.). This allows for automated construction and low-cost mass production.
Most applications can be accommodated by these ready-made rails. However, if a construction project requires custom-length sections, some manufacturers offer rails that can be cut and fitted to the desired length. Since sized rail sections have top rails at 1066 mm (42 in.) and mid-rails at 533 mm (21 in.), they comply with the minimum requirements set by OSHA.
Other options for sized rail sections include:
1. Collapsible railings
If contractors wish to keep sized rail sections unobtrusive, collapsible railings are a good option. They have pivot points on each rail leg, making it easy to fold down the rails and keep them out of sight. To maximize fall protection, outriggers are placed at the start and end of collapsible railings’ runs, positioned at 90-degree angles on the ‘danger side’ of each end.
2. Rails with different leg lengths
Sized rail sections with different leg lengths can adjust to different roof heights without interrupting a run.
3. Customizable safety gates
A gate can be installed to allow access into runs and make it easier for workers to move between the sections divided by rails.
4. Adjustable mid-rail
As the name suggests, an adjustable mid-rail can be fitted to accommodate equipment on roof-line ventilation pipes, stairs, and similar areas. This ensures workers are protected even in areas where rail installation would otherwise be difficult.
5. D-rails or finish rails
D-rails’ cantilever finish allows them to butt up against other surfaces smoothly and avoid jutting edges with the potential to cause injuries.
A thorough description of these structural tubings and fabrications should be included when specifying sized rail sections. Any changes in rail type should be accommodated, especially when considering the different stages a construction project will undergo.
Mechanically assembled or fastened systems are constructed onsite with fittings and fasteners. A section of pipe is used as the vertical stanchion, while the horizontal rail is made of several lengths of pipe joined by connection sleeves. Fittings are used to support the horizontal rail at the stanchions.
Some manufacturers offer inclined or curved pipe stanchions in addition to the vertical variety—these allow the rail to be adjusted according to the architectural design of a building, reducing visibility of it from lower sightlines. When specifying mechanically assembled or fastened systems, a description of the pipes and fittings used should be included.