Grasping non-penetrating fall protection guardrail systems
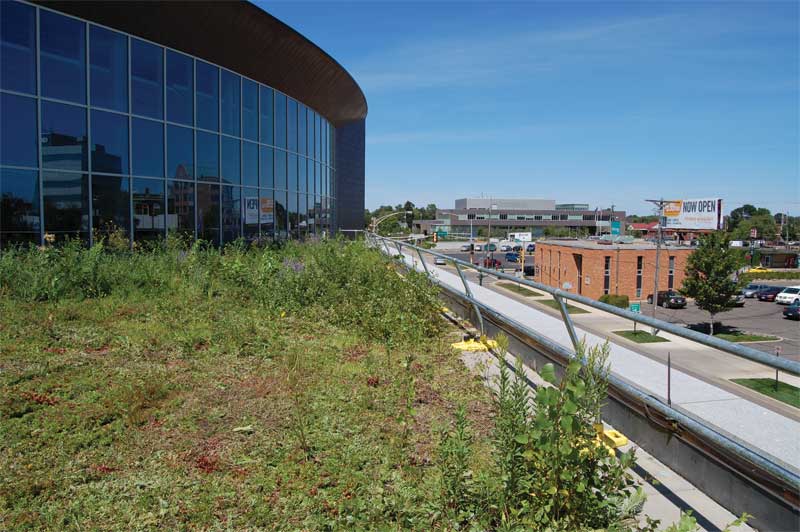
Base support systems
Most non-penetrating guardrails have a base system ballasting the railing. These systems are unique to each manufacturer, so rails from different suppliers cannot be used for the same base. However, a single base can support different rail systems if all are from the same manufacturer.
Bases are the literal backbone of a non-penetrating guardrail system, providing the anchoring mechanism for the rails to meet OSHA’s minimum 90-kg load requirements. They can be manufactured out of cast steel, or can implement PVC pads as a counterbalance.
Bases come in a wide variety of configurations, many of which:
- have four receiver ports to accommodate four stanchions on
a single base; - allow rails to connect in a variety
of directions; - have a built-in toeboard for added safety;
- use a pin or friction knob to secure the rails; or
- come in the form of base plates, which attach the mechanically assembled rail to the roof seams.
Having knowledge of these types of base support systems makes it possible to specify the application of the base with understanding of how the rails and base connect to each other and how the base can be used to do more than support the rails. (For example, hinge posts can be inserted into the receiver posts, to which self-closing gates can be attached.) Most importantly, the base system best fitting current construction needs can be determined.
Finish options
For sized rail sections, one important consideration is finish. Most manufacturers offer various solutions for this, although a ‘safety-yellow’ powder-coat finish is considered the standard. Colors matching common roof and trim finishes are also available for a slight upcharge. If the rail section’s finish needs to be matched with non-standard hues, additional matching fees and setup charges may apply.
If an area needs additional corrosion resistance, galvanized finishes are recommended. Specifications outlining both custom paint and galvanized finishes are not uncommon—often, specifiers will list both in the master specifications and forget to remove whichever they are not using. However, custom paint over a galvanized finish is rarely required and is generally not cost-effective.
When custom colors are requested, using sized rail sections is recommended. Mechanically fastened systems can be custom-painted, but because they are cut to fit onsite, galvanized finish is recommended to keep the cuts from showing corrosion. Painting over galvanized finish also requires additional steps in the finishing process, as well as special handling during assembly to avoid scratching the painted surface.
Mechanically assembled or fastened systems are often specified in a galvanized finish due to the work required for the pipes. For bases, a safety-yellow powder-coat finish is most appropriate, as bases are not usually visible. If the base requires corrosion resistance, however, a galvanized finish may also be used.
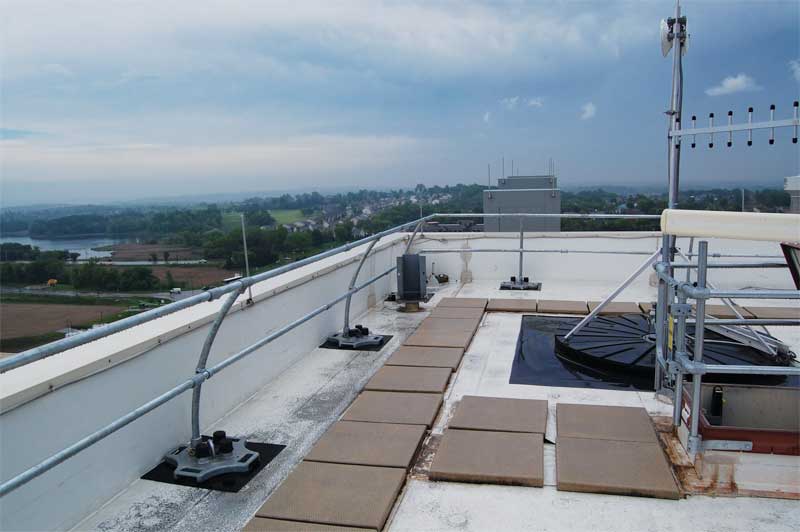
Layout
Layout is one of the areas most often overlooked by architects and specification writers. At the points where non-penetrating guardrails start and end, enough room should be provided for the system to withstand the 90-kg load requirement.
For systems where bases are placed directly under the rail sections, the base runs perpendicular to the leading edge for stabilization of its end. Having a rail outrigger also helps define the ‘safe’ area within the rail section. If the bases are located behind the rail system, components are added to the base to meet the load requirement.
In some instances, outriggers or counterbalancing mechanisms are not required—for instance, when the rail system is ‘closed’ (i.e. when the start and end points are the same) or when the end of the run is directly attached to the building.
Outriggers have the potential to be trip hazards, but most manufacturers use the rail as the element tying the outriggers’ bases to the system, preventing this. Some systems also use counter-balance components that could pose a trip hazard.
Other considerations
Other factors to consider when positioning a rail system include equipment, vents, drains, crickets, seams, and roof undulations on the construction site. The system should be able to accommodate these not only during installation, but also throughout the project’s duration and the life of the building.
Bases should never be positioned on a surface preventing them from staying flat, like seams and crickets. This is especially important with non-penetrating guardrails, which can be derailed if their location is unable to physically support them.
If other concerns arise regarding how a system should be laid out, it is best to contact the manufacturer for assistance.