The nuances of vision glazing color
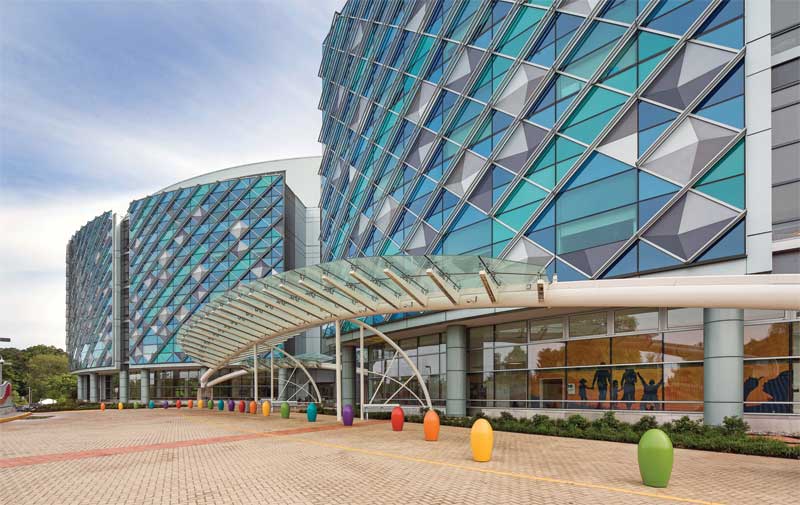
Color measurement
Glass is a unique material in that it has a transmitted color (i.e. what is seen looking through the glass) and a reflected color (i.e. what is seen looking at the glass, usually with some viewing angle). Therefore, what the eye sees is a blending of both the transmitted and reflected colors of the glazing.
A spectrophotometer—a sophisticated instrument made up of a known light source, a sample holder or port, an integrating sphere to collect light, and a known light detector—is used to measure an object’s color. Most types of spectrophotometers can measure both transmitted and reflected color and have built-in software to calculate the measured color of an object and provide numerical L*a*b* data, which can then be compared to the color of other objects.
Glazing color uniformity is formally defined or referenced in several industry standards published by ASTM International. ASTM C1376, Standard Specification for Pyrolytic and Vacuum Deposition Coatings on Flat Glass, and ASTM D2244, Standard Practice for Calculation of Color Tolerances and Color Differences from Instrumentally Measured Color Coordinates, are the building glazing industry standards. They utilize L*a*b* color measurements with the spectrophotometer oriented perpendicular to the glass surface.
ASTM C1376 sets the limit of the exterior color uniformity range for pyrolytic- and vacuum deposition-coated flat glass both within a glazed unit and from one glazed unit to the next. It is important to note visually observable differences are possible within this specified range. ASTM C1376 also notes glass may have a perceived color difference when viewed from different angles. This is a common phenomenon and does not necessarily indicate a reason to reject the product.
How low-e coatings affect light and color
Low-e glass is often specified for IGUs and curtain wall assemblies because of its ability to transmit light and diminish heat gain, thereby increasing the energy efficiency of buildings. This glass type is formulated with multiple ultra-thin layers of materials—mainly silver and other metal oxides—on the surface of clear and tinted glass substrates of varying thicknesses.
Most often, this coating is deposited on the surface by magnetron sputter vacuum deposition (MSVD)—a high-tech process in which multiple nanolayers of heat- and light-controlling materials are applied to the glass surface one atom at a time. This activity takes place in a chamber vacuumized to levels equivalent to those of outer space. Accurate gas flow controls and precise monitoring are critical to successfully depositing MSVD coatings—whose thicknesses are typically measured in angstroms (Å)—on the surface of the glass substrate. The optimal coating stack is only about 0.0002 times as thick as the glass lite onto which it is coated.
Chemical vapor deposition (CVD), an alternative, cost-effective coating process, is used more for adding tinted or reflective coatings, which can also have some low-e properties, to a glass substrate. The CVD process is typically conducted at atmospheric pressure (i.e. no special high-vacuum chamber is required) and frequently with heat, depositing coatings onto hot substrate glass. When materials are fed into the CVD chamber or sprayed onto the hot glass, a chemical reaction occurs and deposits form on the glass surface while byproducts are taken away in the exhaust. The types of materials better suited to the CVD process are somewhat limited, and the coating layer thickness controls are not as good as they are with the MSVD process. Therefore, the types of resultant coatings are also somewhat limited to tinted and/or reflective, and the low-e properties are not as good as with silver-based MSVD coatings.
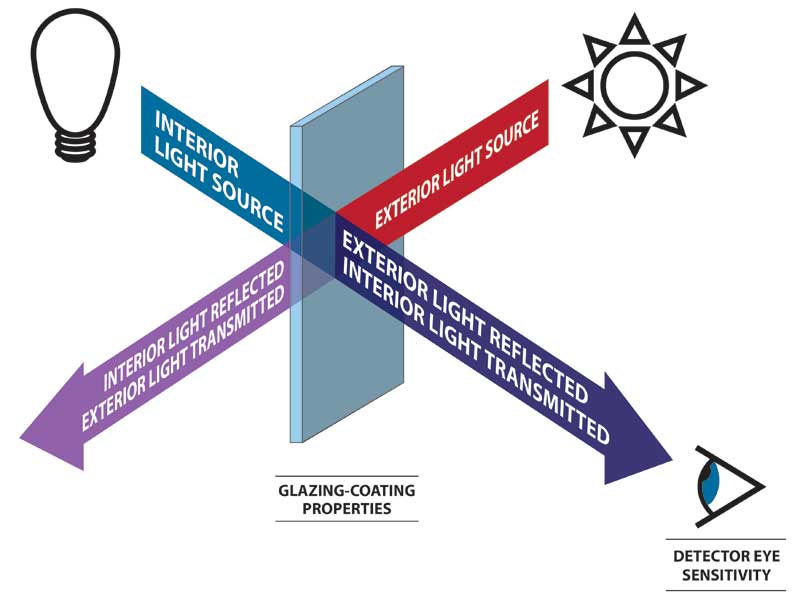
Even at these low levels of thickness, low-e coatings affect the light that passes through, is absorbed by, or reflects off of them. The interaction between light, the coated glass, and the eye of the person looking at the glass relates directly to color uniformity, as seen in Figure 3.
Low-e coatings can also increase the amount of reflection, which adds to the perceived color, especially when viewed from the building exterior. During certain conditions, such as a cloudy day, the reflected color appearance may dominate, particularly when viewed against the dark background of an unfinished building interior. Ambient conditions also change with the time of day as well as the angle of the sun, depending on the viewing perspective and whether one is seeing direct or indirect sunlight reflecting in the glazing.
However, once construction of the building is complete, the appearance of the glazing will change because the background and light coming from behind the glass emphasize transmitted color and mute reflected color. Consequently, color differences visually perceived before construction is completed will often become more muted once the building is finished.