Put penetrations to the test: The effect of cladding attachments on air and water barriers
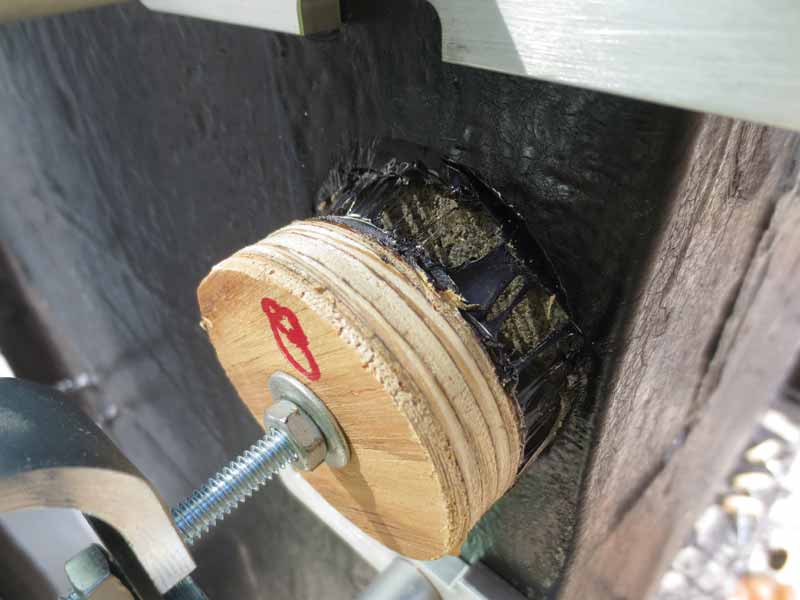
Photos courtesy SmithGroup and RRJ
Field testing
While there are currently no standard field tests specifically for quantifying localized airtightness and watertightness of in-situ AWBs, there are exterior enclosure consultants using the following tests, or some combination thereof, to validate and evaluate, and promote quality assurance/control (QA/QC) efforts for the installed conditions:
- ASTM D4541, Standard Test Method for Pull-Off Strength of Coatings Using Portable Adhesion Testers;
- ASTM E783, Standard Test Method for Field Measurement of Air Leakage Through Installed Exterior Windows and Doors;
- ASTM E1186, Standard Practices for Air Leakage Site Detection in Building Envelopes and Air Barrier Systems; and
- ASTM E1105, Standard Test Method for Field Determination of Water Penetration of Installed Exterior Windows, Skylights, Doors and Curtain Walls, by Uniform or Cyclic Static Air Pressure Difference.
The 2009 version of ASTM D4541 is commonly used to evaluate bond strength, but does not address air or water leakage directly, as it is an adhesion test only. However, it can be considered as a first step in the quality assurance process for the AWB. This test can provide information indicating the material is installed as intended, for a given substrate without any influence of a fastener or penetration (Figure 5). If this type of test is included as a project requirement, design and construction professionals should also consider indicating the bond strength desired for field testing. Manufacturers must be consulted prior to testing, and often will provide laboratory test results, but anticipated field values may be harder to obtain. Another consideration when incorporating this test method is variations in results can occur based on the tester and disc size used. To address some of these concerns, the Air Barrier Association of America (ABAA) has initiated research efforts to compile and analyze available data from audit reports to offer guidance, as well as to develop a test standard tailored specifically to air barrier adhesion and to standardize the approach and equipment.
The next step might be to consider localized, qualitative air leakage testing by performing ASTM E1186. It offers multiple options and procedures within one standard. The Chamber Depressurization in Conjunction With Leak Detection Liquid (“bubble gun”) and the Chamber Depressurization/Pressurization in Conjunction With Smoke Tracers are two tests often included in the field QA/QC plan.
The “bubble gun” is a simple and efficient field test to provide information related to airtightness of fastener penetrations. Air leakage detection fluid is applied over a fastener penetration in the AWB and then a pressure differential is created (Figure 6). The appearance of bubbles in the detection fluid indicates an air path is present (Figure 7).
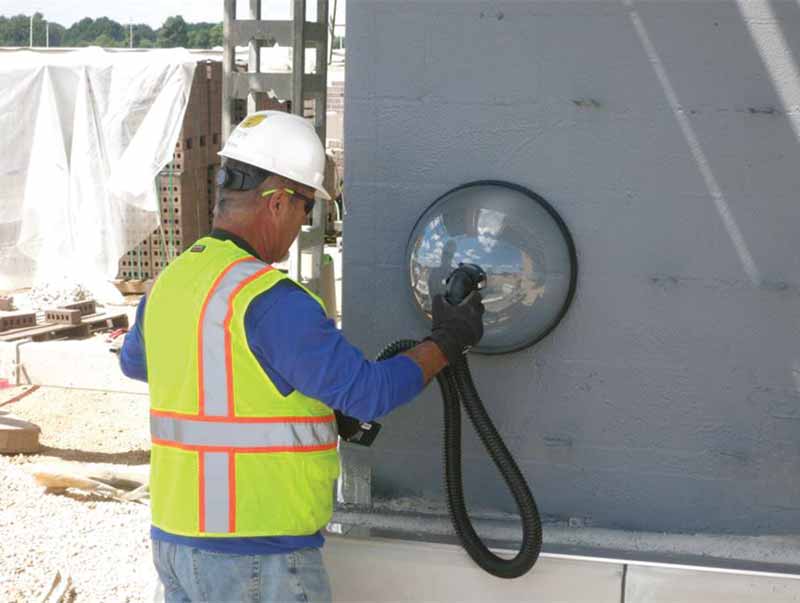
The (de)pressurized smoke tracer test requires a pressure differential of a large area, often necessitating a chamber. This test has the ability to qualitatively evaluate several penetrations at one time. ASTM E783 and ASTM E1105 also utilize a pressure differential chamber, so if those methods are already included as a part of project parameters, smoke tracer tests can be completed easily and efficiently.
ASTM E783 is commonly employed to quantify the air leakage of the field-installed window or door condition, but can be modified to evaluate other enclosure components such as air barrier assemblies. The results from this field test may be compared against the published assembly air leakage rate determined by ASTM E2357 in the laboratory, if similar conditions are evaluated.
The final test for consideration is related to water leakage. ASTM E1105 applies a water spray at the exterior face of an assembly at a required rate of
3.4 L/m2/min (5 g/ph/sf) with a specified air pressure differential. During testing, the interior face of the test area is inspected for water leakage. Under the published method, testing continues for 15 minutes, but consideration can be given to longer durations under specific conditions.
The size of the test areas, the frequency of performing the various tests, and the pressures applied for each of the test types should be considered for inclusion in project documents. Additionally, the time at which these tests are completed, as well as protocols to address failures, are also important considerations for design and construction professionals. Often, testing is completed once the cladding is installed. However, valuable information can be obtained when testing is completed after the installation of the attachments, but prior to the cladding. This is important to identify deficiencies early on, and to easily repair issues if discovered. While this article focuses on in-situ testing, mockups can also be a useful tool to allow testing to be performed prior to the commencement of large-scale implementation (Figure 8). It is also recommended design and construction professionals consider including an outline for the process to address any deficiencies identified during testing, the extent of repair needed, as well as if any additional testing is necessitated.
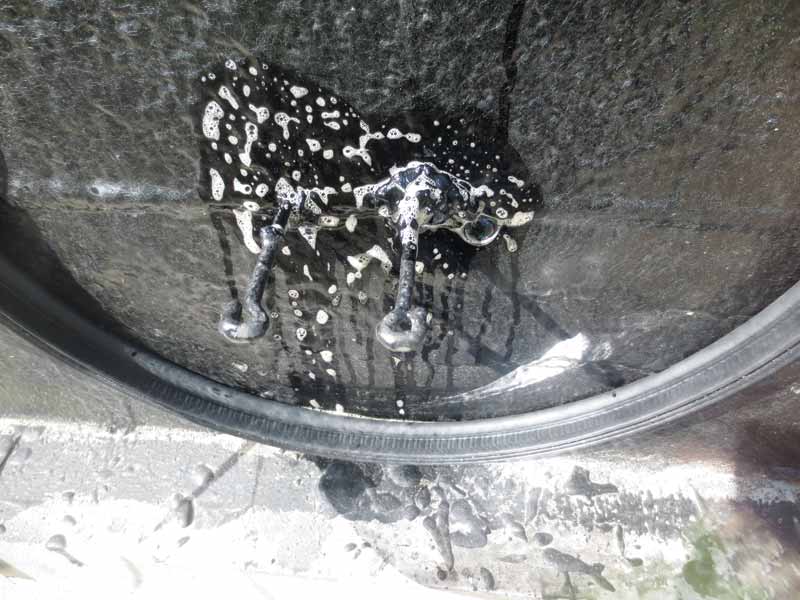
Installation considerations
One may also seek other industry references when it comes to installation considerations of fasteners penetrating the AWB, but resources are limited. Some AWB manufacturers provide guidance for use and reference on the detailing of fasteners, which may establish minimum requirements, but may not produce durable long-term installations. These differences in practices can create problems related to bidding projects, inspecting installations, and durability of the wall assembly. The authors suggest the following can be considered for inclusion as execution requirements (Figure 9):
- use self-tapping screws (i.e. makes its own hole as it is installed);
- employ fasteners with heads larger than the diameter of the shank;
- use fasteners with the point no larger than the diameter of the shank;
- install the fastener into a solid substrate;
- install the fastener perpendicular to the surface as variances can create a larger hole than the fastener, producing avenues for air and moisture as the membrane may not have the ability to seal around the fastener;
- completely set the fastener so the head is compressed against the membrane, resulting in a gasketing effect as mentioned previously;
- set fasteners and cladding accessories in sealant (especially with self-tapping screws); and
- apply sealant over the fastener head.
Research efforts
Given the limited resources, there is a need to develop installation methods that will provide durable and resilient solutions, as well as consensus test standards to validate the airtightness and watertightness of the as-built conditions.
The ABAA research committee and ASTM have both initiated efforts to address these issues and are in the process of developing new test methods to evaluate air/water leakage through fasteners and cladding attachments. The committees in both organizations include representation from manufacturers, architects, researchers, and industry professionals.
Under development within ABAA is a multistep process that may include a large-scale wall assembly test similar to ASTM E2357, but with the inclusion of a water penetration test similar to ASTM E331. A “sub-assembly” test to isolate individual fasteners or attachment devices in a singular test is also being discussed, with the goal intended to deliver product-specific results that can be substituted into the large-scale wall assembly test.
These tests will include variations on fastener installation methods, several types of preconditioning of the specimens, and testing at various pressure differential levels. With the information learned from this study, penetrations through enclosure elements can be better addressed to provide air and moisture management. ABAA is also beginning the process to develop field air and water tests similar to those previously indicated in this article but specifically for AWBs. ABAA and its research committee endeavors to further study this issue to produce meaningful data to assist the design and construction community. Additional studies are also being considered for laps, seams, and joints as similar AWB performance concerns to the fasteners may occur at these features.
Conclusion
Available guidelines for detailing and testing the installed AWB with cladding attachments can be limited, and installation practices are not consistent from project to project. Further, test methods that are currently being used by manufacturers and industry professionals may not be representative of built conditions. To further this point, most of the testing and terminology discussed earlier describes the fastener’s performance upon installation in a laboratory, rather than the long-term durability of the installed condition. A building can experience numerous and significant movement while in service which can have an effect on the air and watertightness of the fasteners securing exterior claddings and penetrating the AWB. It is recommended design and construction professionals consider these issues when dealing with the performance of penetrations through the AWB.
Sarah K. Flock, CDT, AIA, is an associate principal at Raths, Raths, and Johnson (RRJ). She has more than 15 years of architectural experience in water/moisture intrusion investigations, repair design, and field testing of distressed structures, nonperforming buildings, and material systems. Specializing in building enclosure assessment, Flock has performed hygrothermal modeling to analyze a wide range of projects involving various types of building materials and systems. Her experience has involved peer review of building enclosures and assemblies to ensure the designs meet codes and standards for energy efficiency and environmental performance. Flock is the co-chair of the research committee and on the board of directors for The Air Barrier Association of America (ABAA). She can be contacted via e-mail at skflock@rrj.com.
Andrew Dunlap, AIA, CDT, LEED AP, NCARB, is leader of the building technology studio at SmithGroupJJR. His primary work experience is in the analysis and development of exterior building enclosures including roofing, skylights, windows, curtain walls, rainscreen/cavity walls, and waterproofing. Dunlap regularly participates in reviewing and validating building designs for energy code compliance or to provide design options for exceeding code requirements. He received his B. Arch, B.S. in mathematics, and M. Arch degrees from the University of Detroit Mercy. Dunlap is the co-chair of ABAA research committee and is a member of the board. He can be reached at andrew.dunlap@smithgroupjjr.com.