Specifying the right resinous flooring system
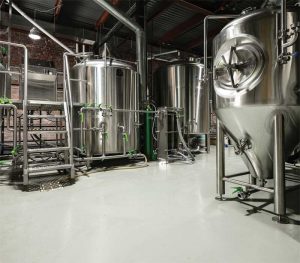
Over time, flooring contractors have modified the double-broadcast floor installation by replacing the first broadcast with a loose “slurry” comprising the coating liquids and a reduced aggregate load. By substituting the first broadcast with the slurry technique, productivity is increased, and installation times are shortened. A second broadcast is still applied for additional thickness, followed by applicable grout- and top-coats.
Broadcast/laminate flooring systems are commonly installed where long service life is required, such as institutional facilities like healthcare, education, or correction, as well as commercial projects and even manufacturing environments. Aesthetic options range from solid colors to decorative quartz and flake.
Mortar flooring systems
These heavy-duty systems are most often used where extreme durability is needed. A mixture of aggregates and coating liquids, these systems are typically trowel applied at a thickness of 6350 μm (250 mils) DFT and then topcoated to seal the mortar and provide additional durability.
Mortar floors are more costly due to the increased material use, and slower technique of trowel application, relegating them to areas of high abuse. Exceptional resistance to impacts, abrasion, and heavy traffic make mortar floors good choices in manufacturing and processing facilities. Mortar flooring systems are generally installed as a solid color, but decorative quartz is sometimes employed for enhanced visual appeal.
Getting the chemistry right
Once the type of system is determined, the next step is to identify the actual coating products. This is best done by categorizing them into the basic chemistry groups most often used in floor coatings, such as epoxies, polyurethanes, and other specialty products.
Epoxy
Epoxies are the workhorses of the coating world. They are known for good adhesion, compressive strength, chemical resistance, and overall durability, all at a moderate cost. Epoxy floor coatings can be solvent- or water-based, but are most commonly offered as solvent-free, 100 percent solids formulations.
Epoxies will yellow with age and can be degraded by ultraviolet (UV) light, so aesthetic considerations should be made based on desired appearance. Often, epoxy systems are topcoated with more color stable coating types, such as aliphatic polyurethanes.
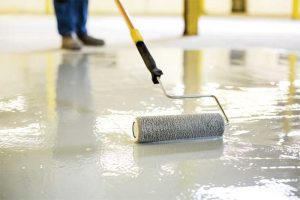
The two most commonly encountered flooring epoxies are polyamine and novolac. Polyamine epoxies are by far the most used and offer all the performance characteristics associated with epoxies including moderate to good chemical resistance. For more extreme chemical exposure, a novolac epoxy may be required. Novolacs have a tighter cross-linked film, which improves chemical resistance. However, they tend to be more expensive and can be susceptible to greater yellowing, so are only used as exposure conditions dictate.
Polyurethane
If epoxies are the workhorses of the coating world then polyurethanes or, more specifically, aliphatic polyurethanes, are the show horses. Aliphatic polyurethanes have excellent color stability and resistance to UV light, and tend to showcase good chemical and abrasion resistance. However, they are typically applied as a thin topcoat of 50-127μm (2 to 5 mils) DFT.
Aromatic polyurethanes are a more industrial variant of the chemistry type. Surrendering the color stability of their aliphatic cousins, aromatic urethanes gain chemical resistance and improved durability. There is a common floor product that combines the characteristics of aromatic polyurethane with the toughness of concrete. Called “urethane-modified concrete,” these products were originally developed and marketed to industrial and processing facilities where a durable floor topping with exceptional resistance to severe freeze-thaw cycling was needed. However, over time, flooring contractors began substituting 100 percent solids epoxies with these products in more commercial and architectural applications because of their fast cure, great adhesion, and tolerance to moisture vapor transmission (MVT). As with epoxies, aromatic polyurethanes are topcoated to improve the system’s appearance.
Specialty products
The coating industry is full of products that do not fall neatly into the epoxy or polyurethane categories.
Methyl methacrylate (MMA) is a fast curing chemistry that is tolerant to cold temperatures during application and cure. For this reason, it is often used where installation must be completed as soon as possible or if the space is unconditioned, even exterior. This cure speed comes with a very high odor, and can only be installed by a specially trained crew. Due to this, coating manufacturers have introduced alternatives to MMA, which includes polyaspartics that combine the speed and color stability of MMA without the offensive odor.
Vinyl esters are an option when specifiers need industrial coatings resistant to chemicals, particularly acids, and are sometimes used within a flooring system. Varieties include thin-film, mortars, and even mat reinforcements. This specialty niche system is relegated to industrial areas exposed to the splash and spillage of chemicals and acids.