Ensuring the quality of thin brick veneer installations
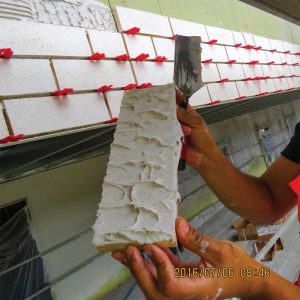
The QC requirement for the Brickyard Project was 95 percent thin-set contact had to be achieved with voids no larger than 1290 mm2. Further, three random and recently installed thin bricks out of 150 had to be removed and documented by the QC inspector. If any of the bricks did not meet the requirement, three more had to be removed and checked. If any of these bricks failed to meet the requirement then the entire group of 150 thin bricks had to be replaced at the installer’s expense. This QC provision is consistent with ANSI A108.5, Installation of Ceramic Tile with Dry-Set Portland Cement Mortar or Latex-Portland Cement Mortar. Installers should be pulling tiles here and there to verify they are getting adequate adhesive coverage. It is easy for them to remove and replace recently installed tiles. Thin-set can be added to tiles lacking in coverage and they can be promptly reinstalled (Figure 8).
Another key step of the QC process is to inspect and acoustically sound the completed installation after it has cured for seven or more days. On a large project like the Brickyard Campus with small tiles it is more of a systematic random process to sound the thin bricks to detect hollow sounding conditions. Various sounding devices, such as a delamination detection tool (DDT), a 25-mm (1-in.) steel ball bearing, or a metal tool, can be used for this purpose. A hollow sound in itself is not a flaw, but it can be a symptom of a defect such as excessive voids. During this process, the QC inspector is also looking to identify any type of visual imperfection for correction (Figure 9).
Conclusion
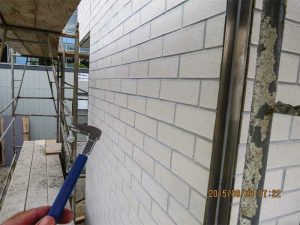
Architects should fully utilize the MasterFormat standard for specifications. It will lead them through a process to properly and thoroughly specify the respective product and its application. Of course, they still need to do the due diligence to vet the application, products, and installation methods. This can be achieved through a QA/QC plan. In this author’s experience, architects and GCs have often said they cannot afford QA/QC services. This responsibility is often transferred to the installation contractor, who, in this author’s opinion, is the least qualified and beyond the scope of their work. The architect and GC are doing a disservice to their client, the owner, if they do not at least specify and recommend QA/QC provisions.
It does not matter who is at fault when there is a problem—everyone ends up paying either in time to defend themselves, money to fix the issue, or with reputation. Therefore, it is in everyone’s best interest to ensure installation specifications are thorough, clear, and unambiguous.
This author has never investigated a tile, brick, or stone failure where all the industry standards and manufacturers’ instructions were followed. The problem is never due to a single deficiency but is always a case of compounding problems. Simply put, the key to a successful thin brick installation is to follow industry standards and to write good specifications. MasterFormat and SectionFormat provide the structure for quality specifications that when used correctly and thoroughly can limit both the designer’s (and the client’s) risk and liability when thin brick, tile, and stone applications are specified.
Donato Pompo, CTC, CSI, CDT, MBA, ITS, is the founder of Ceramic Tile and Stone Consultants (CTaSC) and the University of Ceramic Tile and Stone (U of CTS). He has more than 35 years of experience in the ceramic tile and stone industry from installation and distribution to manufacturing of many installation products. Pompo provides services in forensic investigations, quality control (QC) for products and installation methods, training programs, testing, and onsite inspection. He received the 2012 The Construction Specifier Article of the Year. Pompo can be reached at donato@ctasc.com.