Maintaining continuity: Keeping air/moisture barriers continuous at movement conditions
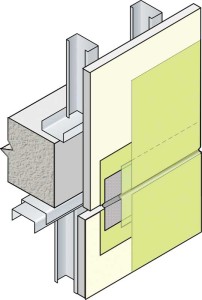
Self-adhered flashings
Unquestionably, the most popular products used for continuity of air and moisture barrier systems are self-adhered membranes. Among these products’ many advantages is their simplicity. The concept of taping over an opening to stop air and water moving in is straightforward, resonating on a very basic level—tears and holes can be fixed with tape.
Beyond the obvious, there are numerous features that make sense with self-adhered membranes. Typically the most economical option, they come in all different shapes and sizes, but are usually very manageable and not too heavy. They have a convenient uniform thickness throughout the roll to ensure one knows exactly how much material is being used. The carrier sheet is usually flexible so it can be bent, folded, and stretched; the sheet itself can be made up of any variety of materials to offer different performance characteristics. Further, the adhesives themselves have come a long way over the years, and now feature different chemistries boasting their own pros and cons.
Once the self-adhered membrane is put in place, a very aggressive bond should occur. Therefore, regardless of the type of building being designed or the climate it will endure, there is likely some version of suitable self-adhered membrane.
Concerns about self-adhered membranes do exist, though. In particular, installation is not as simple
as it seems. In most cases, self-adhered membrane manufacturers recommend a primer on the substrate before installation of the membrane begins. Once the surface is primed, the self-adhered membrane can be laid flat onto the surface to create a bridge in the air and a moisture barrier assembly allowing for continuity. Unfortunately, most self-adhered membranes are not meant to be used with first joints larger than 13 mm (1/2 in.), so additional pieces may need to be lapped onto each other to properly move across the transition.
Typically, self-adhered membranes bond well to each other, so there is no need for a primer where two pieces of tape meet. However, many manufacturers recommend an extra step to seal the edges, meaning a mastic may be needed around all outside edges of the self-adhered membrane pieces.
It is important to remember that buildings are geometrically complex, and the more complex they get, the more difficult it is to fit a piece of tape or several pieces of tape together to fit the critical details and keep air and moisture out. When considering inside and outside corners, recessed windows, and any number of pipes sticking out of the side of the building, there may be a few conditions where one must splice, fold, stretch, and counter-flash to not only ensure water is being kept out, but also to ensure there are no wrinkles or fish mouths in membranes that might inadvertently create new problems.
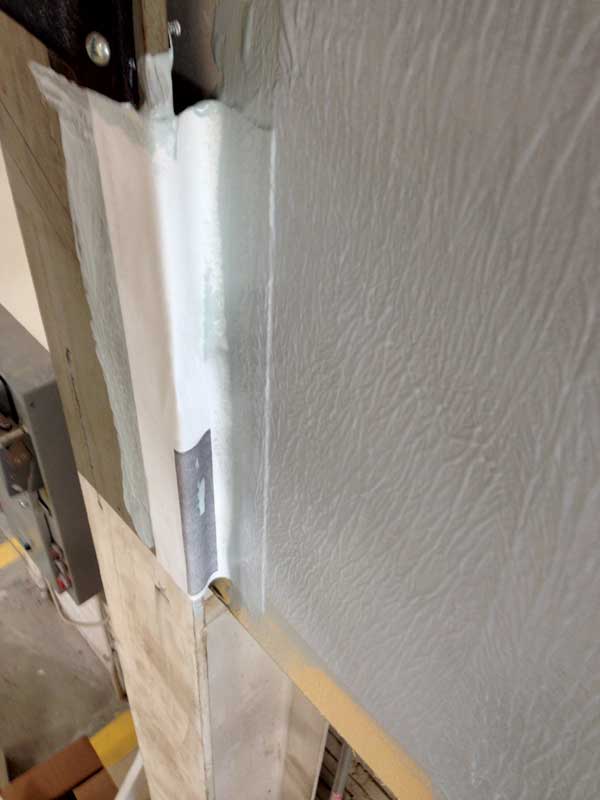
In Joe Lstiburek’s classic article “Stuck on You,” he refers to this need of trying to fit self-adhered flashing tapes to complex geometries as a trade’s need to learn origami to properly wrap openings.3
Further, these products are rarely designed to account for thermal or seismic movement. So, while an aggressive bond between the membrane and the other building components will likely exist if the membrane can be properly applied, the long-term effectiveness of this method may still be questionable.
Silicone solutions
If self-adhered membranes are the most well-known means of maintaining continuity in air and moisture barrier systems, then the combination of silicone sealants and silicone extrusions are probably the most well thought of in terms of durability, function, and overall performance. Silicone sealants are extremely common in construction in areas where a sealant is needed to prevent air and moisture infiltration. While ‘silicone sealant’ is often used as a very broad term, most designers and contractors know these sealants come in a number of different varieties, including high- and low-modulus formulations that may be used for transfer of structural loads or for use in high movement areas, respectively.
Of course, silicone sealants by themselves cannot bridge wider gaps and joints, so they are frequently coupled with silicone extrusions. These extrusions are pre-formed rubberized silicone membranes available in a variety of sizes, styles, and, in some cases, even pre-formed shapes. Silicone extrusions provide excellent flexibility in movement conditions with less likelihood of tearing or loss of adhesion which may be seen when self-adhered membranes are used.
To evaluate this, specific tests have been designed to assess the effectiveness of silicone extrusion and silicon sealant assemblies. ASTM C1518, Standard Specification for Precured Elastomeric Silicone Joint Sealants, is a very rigorous set of tests requiring the silicone sealant and silicone extrusion assembly be tested in various climate conditions. It looks to ensure long-term adhesion and elongation of the assembly without tears or other failures after extensive movement of the assembly.