By Doug Brady
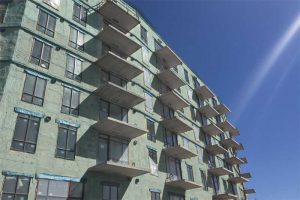
Spray polyurethane foam (SPF) is a building material commonly used in both insulation and roofing applications. The material is manufactured in three core densities, which correspond to the material’s application, or use. The first is open cell insulation, commonly offered at 8-kg/m3 (0.5-lb/cf) density, the second is closed cell insulation, commonly offered at 32-kg/m3 (2-lb/cf) density, and the third is roofing spf, commonly sourced at 40- to 56-kg/m3 (2.5- to 3.5-lb/cf) density. The sprayfoam industry is currently leading an important effort which directly impacts closed cell SPF insulation and roofing SPF. This initiative is a shift away from the use of hydrofluorocarbons (HFC)-based blowing agents to the use of hydrofluoroolefins (HFOs)-based blowing agents.
HFCs are any of several organic compounds composed of hydrogen, fluorine, and carbon, while HFOs are unsaturated organic compounds composed of hydrogen, fluorine, and carbon. Unlike traditional HFCs and their blowing agent predecessors, clorofluorocarbons (CFCs), both of which are saturated, HFOs are olefins, otherwise known as alkenes.
The push toward HFO-based sprayfoam blowing agent technology is the latest step in an ongoing evolution to phase out the use of chemicals known to harm the ozone and climate. In addition to reducing the negative Earth impacts of sprayfoam insulation and roofing materials, there are also product performance and installation considerations. This article will explain the blowing agent shift and why it matters to those considering the specification of sprayfoam for both insulation and roofing applications in commercial building projects.
Blowing agents explained
The Handbook of Foaming and Blowing Agents defines a blowing agent as a substance capable of producing a cellular structure via a foaming process in a material that undergoes hardening or phase transition. Examples of such materials are polymers, plastics, and metals. Two types of blowing agents are distinguished—chemical and physical. Above a certain temperature, or in contact with another specific chemical, it will initiate a chemical reaction that generates a gas. At the same time, a solid plastic is made. The formation of a plastic and the generation of a gas (chemical and/or physical) at the same time make a solid foam structure. Physical blowing agents are metered into the plastics, most frequently in the form of a melt, and they form bubbles by various means.
Blowing agents further divide into endothermic and exothermic foaming agents. Endothermic chemical foaming agents take heat away from the chemical reaction, producing foams with a much smaller cell structure, resulting in improved appearance and better physical properties. Exothermic chemical foaming agents generate heat during the decomposition process. They liberate more gas per gram of foaming agent than endothermic agents and produce higher gas pressure.1
Usually, exothermic blowing agents tend to make larger cells compared to endothermic. In a system, a good balance between endothermic and exothermic blowing agents will make a better dimensionally stable foam. As a further rule of thumb, endothermic blowing agent gives higher R value to the foam.
HFC- and HFO-based, sprayfoam blowing agents are both physical, endothermic blowing agents.
The European FluoroCarbons Technical Committee (EFCTC), a Cefic Sector Group, further defines what makes a good insulation foam blowing agent, stating the “foam blowing agent is selected to provide a closed-cell structure which minimizes heat transfer, in part due to the properties of the foam blowing agent, which is retained within the foam essentially for the lifetime of the foam’s use.”