Protecting those inside: Specifying blast hazard-mitigating windows
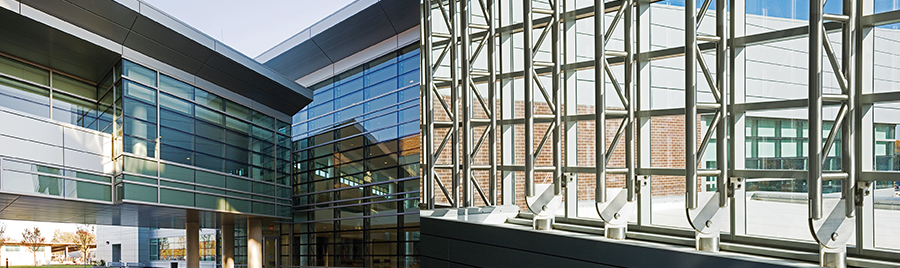
Window framing
Framing members are then designed with deflection not to exceed 1⁄60th of unsupported spans at a load equivalent to two times the glazing resistance determined by ASTM F2248, and connections and anchors sized to absorb and transfer this load to the building structure. Calculations use allowable stress or strength design methods similar to conventional design for wind load.
As potentially less-conservative alternatives to the simplified equivalent three-second-duration design loading, or for higher levels of protection, UFC 2013 allows dynamic analysis using computer finite element modeling to predict how the total assembly will respond. Dynamic analysis offers a significant opportunity to optimize design through fine-tuning system parameters to meet the needs of a specific project—saving material, minimizing fabrication costs, and facilitating easy installation. Testing of representative mockups is also allowed.
Determination of applicable level of protection, standoff distance, and charge weight is the responsibility of the owner’s security/blast consultant/architect; and not that of the window manufacturer or installer. Given these parameters, all calculations should be prepared by a registered professional engineer directly contracted by, or in the employ of, the manufacturer or glazing subcontractor.
It is imperative calculations address specific project requirements, including all framing materials to be furnished. Calculations from other projects, non-representative test results on other systems, or other qualitative analysis generally are unacceptable as a substitute for project-specific calculations.
While project-specific calculations indicating adequacy of framing connections and anchorage must be provided, static analysis of dry-glazed systems is inadvisable. All frame-to-frame connections and connections to the building must be designed using ASTM F2248 under the assumption the glazing fails before the frame members and their connections. To ensure this, connections must be designed to two times the glass load resistance if the maximum air-blast pressure is greater than half the glass load resistance. If pressure is less than half the glass load resistance, connections must be designed to two times the glass load resistance.
Allowable stresses are published by the Aluminum Association, American Institute of Steel Construction (AISC), Allied Construction Industries, or American Iron and Steel Institute (AISI) for the respective materials used in each component. Geometry and connection configuration must be taken into account when calculating loads on connections and anchors.
In addition to blast loads, all components must be designed to satisfy applicable code requirements for adequate glass support, wind, and gravity loads.
Testing
Shock-tube or open-arena testing at a laboratory specifically accredited for blast testing may be acceptable in lieu of static or dynamic analysis, if sizes and configurations tested comply fully with the limitations of U.S. Army Corps of Engineers/U.S. Naval Facilities Engineering Command/Air Force Civil Engineer Center/National Aeronautics and Space Administration (USACE/NAVFAC/AFCEC/NASA) Unified Facilities Guide Specification (UFGS). This specification cites ASTM F1642, Standard Test Method for Glazing and Glazing Systems Subject to Air-blast Loadings, as the basis for alternative compliance.
It is vital to realize UFGS allows only relatively minor departures in size and configuration between tested windows and those to be used for any given project, which can be 25 percent smaller or 10 percent larger in area than the test specimens. ASTM F1642 requires a minimum of three specimens for each pressure and impulse combination. One should be skeptical of claims ‘standard’ windows have been pre-tested to meet specific project requirements.
Energy matters
Like other federal agencies, DoD and design teams working on military buildings of all kinds are committed to complying with high-performance building laws and executive orders. As noted in the National Academies’ “Energy-Efficiency Standards and Green Building Certification Systems Used by the Department of Defense for Military Construction and Major Renovations:”
Specifically, DOD’s policy is that all new building design and construction and all major renovation projects should conform to the Guiding Principles for Federal Leadership in High Performance and Sustainable Buildings (as outlined in Executive Order 13423) and must meet a LEED-Silver rating or equal at a minimum. Beginning in fiscal year (FY) 2012 for projects in the planning stage, the sum of energy and water efficiency credits must equal or exceed 40 percent of the points required for a LEED Silver or equivalent rating.
Blast hazard mitigation requires no compromise in energy-efficiency goals. Manufacturers offer designs that employ sustainable features such as:
- operable vents—both outward-projecting and inward-projecting—for natural ventilation;
- large daylight openings for views, a connection to the outdoors, and natural daylight-harvest using dimmable artificial lighting; and
- spectrally selective, low-emissivity (low-e) coatings on triple-insulating glass for low thermal transmittance (U-factor) and low solar heat gain coefficient (SHGC).
The mandated project-specific design provisions of the new UFC 2013 are especially conducive to optimization of framing and glass selection to suit the sustainable design needs of specific sites, building orientation, and programmatic needs.